图书介绍
人机系统精细化管理手册PDF|Epub|txt|kindle电子书版本网盘下载
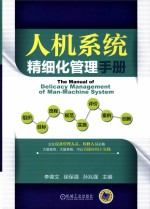
- 李葆文,徐保强,孙兆强主编;马迅,王章明,余培峰,柳草,蔡宗照,蒋坛军,车贺威,刘大永,张洪飞,袁斯殷,陆婉莹,甘艳慧,郭智聪参编 著
- 出版社: 北京:机械工业出版社
- ISBN:9787111471929
- 出版时间:2014
- 标注页数:643页
- 文件大小:182MB
- 文件页数:671页
- 主题词:人-机系统-应用-企业管理-手册
PDF下载
下载说明
人机系统精细化管理手册PDF格式电子书版下载
下载的文件为RAR压缩包。需要使用解压软件进行解压得到PDF格式图书。建议使用BT下载工具Free Download Manager进行下载,简称FDM(免费,没有广告,支持多平台)。本站资源全部打包为BT种子。所以需要使用专业的BT下载软件进行下载。如BitComet qBittorrent uTorrent等BT下载工具。迅雷目前由于本站不是热门资源。不推荐使用!后期资源热门了。安装了迅雷也可以迅雷进行下载!
(文件页数 要大于 标注页数,上中下等多册电子书除外)
注意:本站所有压缩包均有解压码: 点击下载压缩包解压工具
图书目录
第1篇 设备引进前期管理篇4
第1章 设备前期管理总体框架4
1.1 设备前期管理组织职责4
1.1.1 组织职责分工4
1.1.2 系统管理4
1.2 设备前期管理目标和手段4
1.3 设备前期管理工作流程5
1.4 设备前期管理制度规范6
1.4.1 设备规划管理规定6
1.4.2 设备选型决策管理规定6
1.4.3 设备安装调试管理规定6
1.4.4 设备运行初期管理规定6
1.4.5 设备合同管理规定6
1.5 设备前期管理实施细则6
1.5.1 设备招标管理实施细则6
1.5.2 设备工程监理实施细则6
1.5.3 设备监造实施细则6
1.5.4 设备安装实施细则6
1.5.5 设备调试实施细则6
1.5.6 设备验收实施细则7
1.6 设备前期管理评价激励7
1.6.1 评价目的7
1.6.2 评价指标体系7
1.6.3 评价流程7
1.6.4 激励7
1.7 设备前期管理案例分析7
1.7.1 宝钢大型流程设备引进案例描述7
1.7.2 宝钢设备引进优势8
1.7.3 不足8
1.8 设备前期管理创新方向8
1.8.1 可行性研究的突破8
1.8.2 招标选型综合评价决策模型的应用8
1.8.3 安全、低碳、环保成为新时代设备引进的关键要素9
第2章 设备规划和可行性研究11
2.1 规划和可行性研究组织的职责11
2.1.1 构成11
2.1.2 职责11
2.2 规划和可行性研究目标和手段11
2.2.1 预测市场11
2.2.2 知己知彼11
2.2.3 把握方向11
2.3 规划和可行性研究工作流程11
2.4 规划和可行性研究制度规范12
2.4.1 设备规划的主要内容12
2.4.2 设备规划目的与依据12
2.4.3 设备规划可行性分析13
2.4.4 设备投资效益分析13
2.4.5 设备寿命周期费用分析13
2.4.6 设备规划决策流程13
2.5 规划和可行性研究实施细则13
2 5.1 规划组织机构和职责分工13
2.5.2 市场预测小组工作任务描述及其工作流程13
2.5.3 可行性研究小组工作任务描述及其工作流程13
2.5.4 投资效益分析小组工作任务描述及其工作流程13
2.5.5 寿命周期效益分析工作任务描述及其工作流程13
2.5.6 规划报告研讨与汇总13
2.5.7 规划的申报和审批14
2.5.8 规划分解和年度实施计划工作细则14
2.6 规划和可行性研究评价激励14
2.6.1 评价指标体系14
2.6.2 激励14
2.7 规划和可行性研究案例分析14
2.7.1 案例一14
2.7.2 案例二14
2.7.3 案例三14
2.7.4 案例四14
2.7.5 案例五14
2.8 规划和可行性研究创新方向15
2.8.1 第一层面的战略性思考15
2.8.2 第二层面的战略性思考15
第3章 设备选型决策17
3.1 设备选型决策组织职责17
3.1.1 构成17
3.1.2 职责17
3.2 设备选型决策目标和手段17
3.3 设备选型决策工作流程17
3.4 设备选型决策制度规范19
3.4.1 设备选型决策规定19
3.4.2 设备招标管理制度19
3.5 设备选型决策实施细则20
3.5.1 设备选型实施细则20
3.5.2 设备采购招标实施方案20
3.6 设备选型决策评价激励21
3.6.1 选型过程评价指标21
3.6.2 选型结果评价指标21
3.6.3 招标过程评价指标21
3.6.4 招标结果评价指标21
3.6.5 激励21
3.7 设备选型决策案例分析21
3.8 设备选型决策创新方向21
第4章 设备安装调试24
4.1 设备安装调试组织职责24
4.1.1 构成24
4.1.2 职责24
4.2 设备安装调试目标24
4.2.1 安装目标24
4.2.2 调试目标24
4.2.3 验收目标24
4.3 设备安装调试工作流程24
4.4 设备安装调试制度24
4.4.1 设备安装管理制度24
4.4.2 设备调试管理制度27
4.4.3 设备验收管理制度27
4.5 设备安装调试实施细则27
4.6 设备安装调试评价激励27
4.7 设备安装调试案例分析28
4.7.1 案例一28
4.7.2 案例二30
4.8 设备安装调试创新方向30
4.8.1 充分利用社会化安装公司30
4.8.2 用户检修和使用部门的全程参与30
4.8.3 安装调试中的知识管理30
第5章 设备运行初期管理32
5.1 运行初期管理组织职责32
5.1.1 构成32
5.1.2 职责32
5.2 运行初期管理目标和手段32
5.2.1 按照时间承诺达标达产32
5.2.2 掌握设备工艺质量要领32
5.2.3 摸清设备运行调整及维护保养规律32
5.3 运行初期管理工作流程32
5.4 运行初期管理制度规范33
5.4.1 设备运行初期组织职责分工33
5.4.2 设备运行初期管理要点33
5.5 运行初期管理实施细则34
5.5.1 设备操作工艺流程图34
5.5.2 设备操作可视化细则34
5.5.3 设备保养可视化细则34
5.5.4 设备运行状态跟踪记录表34
5.5.5 质量控制关键操作指南35
5.5.6 设备检修流程图35
5.5.7 设备初期管理总结模板35
5.6 运行初期管理评价激励35
5.6.1 过程指标35
5.6.2 结果指标36
5.7 运行初期管理案例分析36
5.8 运行初期管理创新方向36
第6章 设备合同管理39
6.1 设备合同管理组织职责39
6.1.1 构成39
6.1.2 职责39
6.2 设备合同管理目标和手段39
6.2.1 目标39
6.2.2 手段39
6.3 设备合同管理工作流程39
6.4 设备合同管理制度规范39
6.4.1 合同谈判规范39
6.4.2 合同签订规范41
6.4.3 合同执行规范43
6.5 设备合同管理实施细则44
6.5.1 合同谈判实施细则44
6.5.2 合同签订实施细则45
6.5.3 合同执行实施细则46
6.6 设备合同管理评价激励46
6.6.1 评价目的46
6.6.2 评价内容46
6.6.3 激励方式46
6.7 设备合同管理案例分析47
6.7.1 案例一47
6.7.2 案例二47
6.8 设备合同管理创新方向47
第2篇 资产台账知识管理篇52
第1章 设备分类与资产编号52
1.1 设备分类与资产编号组织职责52
1.1.1 设备管理部门52
1.1.2 财会部门及设备使用单位52
1.2 设备分类与资产编号目的52
1.3 设备分类与资产编号工作流程52
1.4 设备分类与资产编号原则52
1.5 设备分类与资产编号实施细则53
1.5.1 设备分类53
1.5.2 设备资产编号56
1.6 设备分类与资产编号的评价激励56
1.7 设备分类与资产编号的案例分析57
1.8 设备分类与资产编号的创新方向57
第2章 设备台账和设备卡片59
2.1 设备台账和设备卡片组织职责59
2.1.1 构成59
2.1.2 职责59
2.2 设备台账和设备卡片目的59
2.3 设备台账和设备卡片工作流程59
2.4 设备台账和设备卡片制度规范59
2.5 设备台账和设备卡片实施细则59
2.5.1 建立设备台账59
2.5.2 设备卡片61
2.6 设备台账和设备卡片的评价激励61
2.7 设备台账和设备卡片的案例分析61
2.8 设备台账和设备卡片的创新方向62
第3章 设备档案与资料管理64
3.1 设备档案与资料管理组织职责64
3.1.1 设备管理部门64
3.1.2 企业维修部门和生产车间(分厂)64
3.2 设备档案与资料管理目标64
3.3 设备档案与资料管理工作流程64
3.4 设备档案与资料管理要求64
3.4.1 设备档案与资料管理基本要求64
3.4.2 设备档案的编制要求64
3.4.3 收集编制资料注意事项64
3.5 设备档案与资料管理实施细则66
3.5.1 设备档案与资料内容66
3.5.2 设备档案与资料的管理内容67
3.6 设备档案与资料管理的评价激励67
3.7 设备档案与资料管理案例分析67
3.7.1 设备档案管理办法主要内容67
3.7.2 设备资料室管理制度68
3.8 设备档案与资料管理创新方向68
第3篇 赢在基层团队成长篇72
第1章 团队培训72
1.1 团队培训推行组织及职责72
1.2 团队培训的主要内容和目标72
1.2.1 工作现场培训72
1.2.2 集中培训72
1.2.3 好的培训73
1.3 团队培训的工作流程73
1.3.1 公司级别培训的主要流程73
1.3.2 班组培训流程74
1.4 团队培训的制度规范75
1.4.1 确定培训需求75
1.4.2 设计培训内容75
1.5 团队培训的实施细则75
1.6 团队培训的评价与激励75
1.6.1 团队培训的评价75
1.6.2 团队培训的激励76
1.7 团队培训的案例分析76
1.8 团队培训的创新方法77
1.8.1 培训角色的创新77
1.8.2 培训方法的创新77
第2章 团队沟通80
2.1 团队沟通的组织及职责80
2.2 团队沟通的主要内容80
2.2.1 质量管理方面80
2.2.2 设备管理方面81
2.2.3 物料管理方面81
2.2.4 关于人员方面的沟通81
2.2.5 其他方面涉及的沟通管理81
2.3 团队沟通的工作流程81
2.4 团队沟通的实施细则84
2.4.1 文件(含文书)沟通84
2.4.2 会议沟通84
2.4.3 沟通的反馈85
2.5 团队沟通案例分析85
2.6 团队沟通的创新方向86
2.6.1 班组例会86
2.6.2 橱窗展示86
2.6.3 绩效面谈86
2.6.4 班组长谈心86
2.6.5 非正式的随时沟通86
第3章 有氧活动88
3.1 有氧活动的组织职责88
3.2 有氧活动的主要内容和目标89
3.2.1 OPL的主要内容89
3.2.2 OPS的主要内容89
3.3 有氧活动的工作流程90
3.3.1 OPL的工作流程90
3.3.2 OPS的工作流程90
3.4 有氧活动的制度规范90
3.5 有氧活动的实施细则90
3.5.1 OPL的实施细则90
3.5.2 OPS的实施细则92
3.6 有氧活动的评价与激励92
3.6.1 员工编制的OPL92
3.6.2 员工编制的OPS96
3.6.3 奖励100
3.7 有氧活动的案例分析100
3.8 有氧活动的创新方向101
3.8.1 OPL展示形式创新101
3.8.2 OPL概念的延伸101
3.8.3 OPS应用方式的创新102
3.8.4 从OPS到小组改善102
第4章 团队激励107
4.1 团队激励的组织及职责107
4.1.1 组织的构成107
4.1.2 组织的职责107
4.2 团队激励的主要内容和目标107
4.2.1 正向激励107
4.2.2 负向激励108
4.2.3 定期激励108
4.2.4 不定期激励108
4.3 团队激励的工作流程108
4.3.1 定期激励108
4.3.2 不定期激励108
4.4 团队激励种类的定义108
4.5 团队激励的实施细则109
4.5.1 员工激励制度具体内容109
4.5.2 员工激励制度需求的提出109
4.6 团队激励的效果评价与激励109
4.6.1 评价指标体系109
4.6.2 激励110
4.7 团队激励案例分析110
4.8 团队激励的创新方向110
4.8.1 团队激励的活性化110
4.8.2 团队激励的需求化111
4.8.3 团队激励的生活化111
4.8.4 团队激励的菜单化112
第5章 团队看板115
5.1 团队看板的组织职责115
5.2 团队看板的主要内容和目标116
5.3 团队看板的工作流程116
5.4 团队看板的制度规范编制117
5.4.1 目标分解展示板117
5.4.2 文化士气看板118
5.4.3 质量控制看板118
5.4.4 设备计划保全日历119
5.4.5 区域责任图119
5.4.6 安全看板119
5.4.7 疑难点清单120
5.4.8 班组管理现况板121
5.4.9 QC工具与改善121
5.4.10 小组活动板122
5.4.11 TnPM诊断现况板122
5.5 团队看板的实施细则和工作要求123
5.5.1 看板版式及内容要求123
5.5.2 看板管理的具体要求123
5.5.3 看板信息的更新124
5.5.4 看板的监察与维护124
5.6 团队看板的评价和激励124
5.7 团队看板的案例分析124
5.8 团队看板的创新方向125
第6章 团队领导127
6.1 团队领导的组织职责127
6.1.1 按照主管管理的五大职责分类127
6.1.2 按照生产的管控目标分类127
6.1.3 按生产要素分类127
6.1.4 八大修炼128
6.1.5 结果是以过程为导向128
6.2 团队领导的目标128
6.3 团队领导的工作流程129
6.4 团队领导的制度规范130
6.5 团队领导的工作细则130
6.5.1 本部门工作要点分时段制订131
6.5.2 上班前该做什么?131
6.5.3 生产前准备要点131
6.5.4 生产过程中工作要点(人)131
6.5.5 生产过程中工作要点(机)131
6.5.6 生产过程中工作要点(料)131
6.5.7 生产过程中工作要点(法)132
6.5.8 生产过程中工作要点(环)132
6.5.9 生产过程中工作要点(品质)132
6.5.10 生产过程中工作要点(士气)132
6.5.11 信息管理132
6.5.12 下班前工作要点133
6.5.13 其他专题会议与人选133
6.5.14 其他专业项目的工作133
6.6 团队领导的评价和激励134
6.6.1 团队领导的评价134
6.6.2 团队领导的激励137
6.7 团队领导的案例分析138
6.7.1 团队领导职务说明书(车间主任级)138
6.7.2 团队领导每日工作细分案例139
6.8 团队领导的创新方向147
6.8.1 团队领导者的角色变革147
6.8.2 团队领导者知识结构的转变147
6.8.3 团队领导考核方式的转变147
第4篇 精心创造卓越现场篇152
第1章 创造卓越现场——6S152
1.1 6S管理的组织职责152
1.1.1 6S项目推行委员会的主要职责152
1.1.2 6S项目推行小组的主要职责152
1.1.3 6S项目检查小组的主要职责153
1.1.4 各实施小组的主要职责153
1.1.5 公司各级人员在6S活动中的职责153
1.2 6S管理的主要内容与目标154
1.2.1 6S管理的主要内容154
1.2.2 6S管理的目标154
1.3 6S管理的工作流程155
1.3.1 实施6S的阶段155
1.3.2 实施6S的流程155
1.4 6S管理的制度规范编制156
1.4.1 6S责任区域划分156
1.4.2 6S准则(要求、规范)157
1.4.3 6S活动程序157
1.5 6S管理的实施细则和展开步骤158
1.5.1 6S管理的实施细则158
1.5.2 6S管理的展开步骤158
1.6 6S管理的评价与激励159
1.6.1 6S评价的方式分两类159
1.6.2 6S评委评审6S的流程159
1.6.3 自主检查160
1.6.4 6S评审标准160
1.6.5 6S检查结果的处置和改善164
1.7 6S管理的企业案例分析166
1.8 6S管理的创新方向168
第2章 创造卓越现场——清除6H170
2.1 6H的组织和职责170
2.1.1 6H的组织170
2.1.2 6H组织的职责170
2.2 6H管理的主要内容与目标170
2.2.1 6H管理的主要内容170
2.2.2 清除6H的管理目标173
2.3 6H管理的工作流程173
2.4 6H管理的制度规范编制176
2.5 6H管理的查找指引和分析工具177
2.5.1 6H管理的查找指引177
2.5.2 6H管理的分析工具182
2.6 6H管理的评价与激励191
2.6.1 6H改善的评价指标191
2.6.2 6H改善的激励191
2.7 6H管理的企业案例分析191
2.8 6H管理的创新方向192
第3章 可视化管理194
3.1 可视化管理的组织职责194
3.2 可视化管理的主要内容与目标195
3.2.1 可视化管理的目的195
3.2.2 可视化管理的目标195
3.3 可视化管理的工作流程195
3.4 可视化管理的制度规范编制196
3.4.1 可视化推进准备196
3.4.2 可视化的组织职责196
3.4.3 可视化的展开实施检查、评比和激励196
3.5 可视化管理的实施细则和工作要求196
3.5.1 建立推进组织196
3.5.2 制定活动计划196
3.5.3 现场诊断,识别可视化对象清单196
3.5.4 可视化对象实施197
3.5.5 可视化管理手册编制197
3.6 可视化管理的评价与激励197
3.6.1 评价流程197
3.6.2 激励198
3.7 可视化管理的企业案例分析198
3.8 可视化管理的创新方向199
第4章 定置管理202
4.1 定置管理的组织职责202
4.2 定置管理的主要内容与目标203
4.2.1 定置管理的主要内容203
4.2.2 定置管理的目标203
4.3 定置管理的工作流程204
4.4 定置管理的制度规范编制205
4.4.1 定置管理推进准备205
4.4.2 定置管理的组织职责205
4.4.3 定置管理展开实施205
4.5 定置管理的实施细则和工作要求205
4.6 定置管理的评价和激励206
4.6.1 评价流程206
4.6.2 激励206
4.7 定置管理的企业案例分析206
4.8 定置管理的创新方向207
第5篇 全员自主维护保障篇212
第1章 全员自主维护保障总体框架212
1.1 全员自主维护保障组织职责212
1.2 自主维护保障基本目标212
1.2.1 设备功能本质状态改善方面变化212
1.2.2 员工维护技能素质方面变化212
1.2.3 设备小停机快速处理方面变化212
1.3 全员自主维护保障工作流程212
1.3.1 四大流程阶段212
1.3.2 自主维护各阶段主要工作内容213
1.4 全员自主维护规范214
1.4.1 自主维护推进管理办法214
1.4.2 自主维护活动技术标准214
1.5 自主维护实施214
1.5.1 防止人为劣化意识的教育214
1.5.2 设备原理与结构培训215
1.5.3 工具技术准备215
1.5.4 安全防范强化215
1.6 全员自主维护保障评价215
1.6.1 自主维护管理策划能否体现5W2H2C1T原则215
1.6.2 活动过程组织领导的参与程度与职责落实情况216
1.6.3 标准的完整性与可操作性216
1.6.4 自主维护活动要求执行是否到位216
1.6.5 指标是否完成216
1.6.6 自主维护效果评价及推广216
1.7 全员自主维护推进管理案例分析216
1.8 全员自主维护管理的创新方向216
1.8.1 巧用杠杆与灵活维护216
1.8.2 创新方法与综合推进217
第2章 设备清扫219
2.1 设备清扫组织职责219
2.2 设备清扫的目标和主要内容219
2.2.1 设备清扫的目标219
2.2.2 设备清扫主要内容219
2.3 设备清扫工作流程219
2.4 设备清扫作业制度规范220
2.4.1 “谁使用谁清扫”原则220
2.4.2 清扫基准书220
2.5 设备清扫活动实施220
2.5.1 选择清扫点220
2.5.2 安全清扫220
2.5.3 全面清扫221
2.5.4 闭环清扫221
2.6 设备清扫评价221
2.6.1 定期组织考核221
2.6.2 清扫评价标准221
2.7 设备清扫案例222
2.7.1 灰尘遮掩“光眼”导致提升机运行不稳定222
2.7.2 用心对待清扫维护工作222
2.8 设备清扫管理创新222
2.8.1 不断提升设备清扫必要性的认识222
2.8.2 不断创新清扫工具开发223
2.8.3 严格交接班管理考核224
第3章 设备点检226
3.1 设备点检组织职责226
3.1.1 点检定义与分类226
3.1.2 点检工作主要责任部门与岗位职责226
3.2 设备点检目标227
3.3 设备点检工作流程227
3.4 设备点检规范228
3.5 设备点检实施229
3.5.1 编制点检计划229
3.5.2 做好点检准备230
3.5.3 组织点检实施230
3.6 点检评价232
3.6.1 点检要素完备性232
3.6.2 点检实绩情况232
3.6.3 点检激励机制的建立233
3.7 设备点检案例233
3.7.1 钟表点检法233
3.7.2 “五感法”点检233
3.7.3 点检基准实例234
3.8 点检创新236
3.8.1 将可视化管理与防呆手法相结合,广泛运用到点检工作中236
3.8.2 运用现代检测工具,发挥精密检测功效236
3.8.3 融合CMMS信息技术,开发简洁实用的点检流程与手段236
第4章 设备保养239
4.1 设备保养组织职责239
4.1.1 保养定义与分类239
4.1.2 主要部门与岗位职责239
4.2 设备保养目标与内容239
4.2.1 保养目标239
4.2.2 保养内容239
4.3 设备保养工作流程240
4.4 设备保养规范241
4.5 设备保养实施241
4.5.1 编制保养计划241
4.5.2 定人241
4.5.3 定时241
4.5.4 定点242
4.5.5 定方法242
4.5.6 定项目242
4.5.7 定标准243
4.5.8 定记录245
4.6 设备保养管理的评价245
4.6.1 保养计划达成率245
4.6.2 设备故障停机率245
4.6.3 设备完好率245
4.6.4 综合保养考核245
4.7 规范化设备保养管理案例分析245
4.7.1 记录卡定位法245
4.7.2 设备保养维护完好率考核表246
4.8 设备保养探索创新247
第5章 “三闭环”流程实施250
5.1 “三闭环”组织职责250
5.1.1 “三闭环”定义与构成250
5.1.2 “三闭环”维护主要部门职责250
5.2 “三闭环”的目的250
5.3 “三闭环”流程250
5.4 “三闭环”规范251
5.4.1 AM自主维护基准书251
5.4.2 “三闭环”维修综合总基准书251
5.5 “三闭环”实施细则252
5.5.1 AM自主维护闭环开始与深入252
5.5.2 PM专业维护闭环的触发和嵌入252
5.5.3 MP维修预防闭环触发和嵌入253
5.5.4 及时传递维修工单253
5.6 “三闭环”案例255
5.6.1 AM闭环自主设计255
5.6.2 机械维修“请修单”作业法255
5.6.3 清扫点检维保总基准书255
5.7 “三闭环”管理评价257
5.7.1 自主维护技能培训考评257
5.7.2 专业维保实施考评257
5.8 “三闭环”创新257
第6篇 全优规范润滑管理篇262
第1章 润滑六定管理262
1.1 设备润滑六定管理的组织职责262
1.1.1 组织职责分工262
1.1.2 系统管理262
1.2 润滑六定管理的主要内容和目标262
1.2.1 定点262
1.2.2 定人262
1.2.3 定质263
1.2.4 定量264
1.2.5 定法265
1.2.6 定期265
1.2.7 管理目标266
1.3 润滑六定管理工作流程266
1.4 润滑六定管理的制度规范266
1.5 润滑六定管理的实施细则266
1.5.1 设备润滑六定的技术规范266
1.5.2 润滑六定文件的制定流程267
1.5.3 设备润滑作业责任制267
1.5.4 润滑记录规范267
1.5.5 润滑油领用统计规范267
1.5.6 泄漏预防267
1.5.7 润滑故障分析267
1.6 润滑六定管理的评价激励267
1.6.1 评价目的267
1.6.2 评价指标体系267
1.6.3 评价基本流程268
1.6.4 激励268
1.7 润滑六定管理的案例分析268
1.8 润滑六定管理的创新方向268
1.8.1 润滑六定标准与最新的技术相结合268
1.8.2 定量加油的进步268
1.8.3 润滑油定质的优化268
第2章 润滑二洁管理271
2.1 “二洁”管理的组织职责271
2.1.1 组织职责分工271
2.1.2 系统管理271
2.2 “二洁”管理的主要内容和目标271
2.2.1 润滑部位的清洁271
2.2.2 润滑工具的清洁272
2.2.3 润滑“二洁”管理的目标272
2.3 “二洁”管理的工作流程272
2.4 润滑“二洁”管理的制度规范273
2.5 “二洁”管理的实施细则273
2.6 润滑“二洁”管理的评价激励273
2.6.1 评价指标体系273
2.6.2 评价流程274
2.6.3 激励274
2.7 “二洁”管理的案例分析274
2.8 “二洁”管理的创新方向274
第3章 润滑三级过滤管理277
3.1 三级过滤的组织职责277
3.1.1 组织职责分工277
3.1.2 系统管理277
3.2 三级过滤的主要内容和目标277
3.2.1 什么是三级过滤?277
3.2.2 三级过滤的重要意义277
3.2.3 三级过滤的实现手段277
3.2.4 在用油的过滤278
3.3 三级过滤的工作流程279
3.4 三级过滤的制度规范279
3.4.1 三级过滤管理规定279
3.4.2 润滑油的再生使用管理规定279
3.4.3 三级过滤的培训279
3.5 三级过滤管理的实施细则279
3.5.1 润滑油的定期监测规范279
3.5.2 润滑过滤装置280
3.5.3 滤芯管理规范280
3.5.4 润滑培训的流程规范280
3.6 三级过滤的评价激励280
3.6.1 三级过滤评价指标280
3.6.2 评价流程280
3.6.3 激励280
3.7 三级过滤的案例分析280
3.8 三级过滤的创新方向280
第4章 换油管理283
4.1 换油管理的组织职责283
4.1.1 组织职责分工283
4.1.2 系统管理283
4.2 换油管理的主要内容和目标283
4.2.1 换油计划283
4.2.2 趋势管理283
4.2.3 换油管理的目标283
4.3 换油管理的工作流程283
4.4 换油管理的制度规范284
4.4.1 润滑油更换管理规定284
4.4.2 废油处理的若干规定284
4.5 换油管理的实施细则284
4.5.1 润滑油更换作业流程284
4.5.2 润滑油更换判断标准284
4.5.3 润滑油使用统计分析流程284
4.6 换油管理的评价激励284
4.7 换油管理的案例分析285
4.8 换油管理的创新方向285
第5章 油液分析与故障诊断287
5.1 油液分析和故障诊断的组织职责287
5.1.1 组织职责分工287
5.1.2 系统管理287
5.2 油液分析和故障诊断的主要内容和目标287
5.2.1 油液分析的作用287
5.2.2 常用的油液分析方法288
5.2.3 油液分析与故障诊断的作用291
5.2.4 故障的趋势管理292
5.2.5 油液取样管理293
5.3 油液分析和故障诊断的工作流程294
5.4 油液分析和故障诊断的制度规范294
5.4.1 油液分析管理294
5.4.2 润滑油取样管理294
5.4.3 故障管理294
5.4.4 油库采样管理294
5.5 油液分析和故障诊断的实施细则294
5.5.1 油液分析取样点确定294
5.5.2 油液化验作业流程295
5.5.3 油品更换参考标准295
5.5.4 故障分析流程295
5.6 油液分析和故障诊断的评价激励295
5.6.1 评价标准295
5.6.2 评价流程295
5.6.3 激励295
5.7 油液分析和故障诊断的案例分析295
5.8 油液分析和故障诊断的创新方向296
第6章 润滑站管理298
6.1 润滑站管理的组织职责298
6.1.1 组织职责分工298
6.1.2 系统管理298
6.2 润滑站管理的主要内容和目标298
6.2.1 公司润滑站管理298
6.2.2 车间润滑站的日常维护299
6.3 润滑站管理的工作流程300
6.4 润滑站管理的制度规范301
6.4.1 润滑站管理制度301
6.4.2 油料采购领用管理规定301
6.4.3 润滑站安全管理制度301
6.5 润滑站管理的实施细则301
6.5.1 油料采购申请流程301
6.5.2 油料领用流程301
6.5.3 润滑站油料化验流程301
6.5.4 润滑站油料化验判断标准302
6.6 润滑站管理的评价激励302
6.6.1 评价标准302
6.6.2 评价流程302
6.6.3 激励302
6.7 润滑站管理的案例分析302
6.8 润滑站管理的创新方向303
第7章 润滑管理体系的评价305
7.1 润滑管理体系评价的组织职责305
7.1.1 组织职责分工305
7.1.2 系统管理305
7.2 润滑管理评价的内容和主要目标305
7.2.1 评价的内容305
7.2.2 润滑管理评价的标准306
7.2.3 评价的目标306
7.3 润滑管理评价的工作流程306
7.4 润滑管理评价的制度规范306
7.4.1 润滑管理体系的评价306
7.4.2 评价的KPI设计原则307
7.4.3 润滑管理评价的周期安排307
7.5 润滑管理评价的实施细则307
7.5.1 润滑管理体系评价标准307
7.5.2 管理体系评价项目配分标准307
7.5.3 评价的项目要素307
7.6 润滑管理评价的激励307
7.7 润滑管理评价的案例分析308
7.8 润滑管理评价的创新方向308
第7篇 检维修系统设计优化篇312
第1章 维修策略设计312
1.1 维修策略设计的组织职责312
1.1.1 组织职责分工312
1.1.2 系统管理312
1.2 维修策略设计的内容和目标312
1.2.1 维修策略设计的内容312
1.2.2 维修策略设计的原则313
1.2.3 常用维修策略313
1.3 维修策略设计的工作流程325
1.4 维修策略设计的制度规范326
1.4.1 设备维修策略设计326
1.4.2 设备维修策略的管理326
1.4.3 维修策略的优化326
1.4.4 维修策略设计的培训326
1.5 维修策略设计规范的实施细则326
1.5.1 设备维修策略设计的要素326
1.5.2 维修策略设计的流程326
1.5.3 设备运行的信息收集类别326
1.6 维修策略设计的评价激励326
1.7 维修策略设计的案例分析327
1.8 维修策略设计的创新方向328
第2章 设备信息采集331
2.1 设备信息采集的组织职责331
2.1.1 组织职责分工331
2.1.2 系统管理331
2.2 设备信息采集的内容和目标331
2.2.1 设备信息采集的内容331
2.2.2 设备信息的分析和故障诊断333
2.2.3 设备信息采集方式的选择335
2.3 设备信息采集的工作流程335
2.4 设备信息采集的制度规范336
2.4.1 点检的管理336
2.4.2 状态监测的应用336
2.4.3 点检的培训336
2.5 设备信息采集的实施细则336
2.5.1 设备点检文件设计的要素336
2.5.2 点检的八定一成管理336
2.5.3 状态监测的设计要素336
2.5.4 培训管理336
2.5.5 故障的诊断流程336
2.6 设备信息采集的评价激励337
2.7 设备信息采集的案例分析337
2.7.1 案例一337
2.7.2 案例二338
2.8 设备信息采集的创新方向338
第3章 维修组织设计341
3.1 维修组织设计的组织职责341
3.1.1 组织职责分工341
3.1.2 系统管理341
3.2 维修组织设计的主要内容和工作目标341
3.2.1 维修组织设计的原则341
3.2.2 常见的维修组织结构特点342
3.2.3 维修组织设计的目标343
3.3 维修组织设计的工作流程343
3.4 维修组织设计的制度规范344
3.4.1 设备维修组织建立的目标344
3.4.2 维修组织设计的原则344
3.4.3 组织设计的实施344
3.4.4 组织设计的效果评价344
3.5 设备维修组织设计的实施细则344
3.5.1 维修组织设计的KPI指标344
3.5.2 维修组织设计的流程344
3.5.3 维修组织考核流程344
3.6 维修组织设计的评价激励344
3.7 维修组织设计的案例分析344
3.8 维修组织设计的创新方向345
3.8.1 维修组织的变革345
3.8.2 维修组织再造过程346
第4章 维修资源配置349
4.1 维修资源配置的组织职责349
4.1.1 组织职责分工349
4.1.2 系统管理349
4.2 维修资源配置的主要内容和目标349
4.2.1 维修资源配置的原则349
4.2.2 维修资源的整合350
4.2.3 维修资源配置的目标351
4.3 维修资源配置的工作流程351
4.4 维修资源配置的制度规范351
4.4.1 自主维护的管理351
4.4.2 专业维修队伍的管理351
4.4.3 委外维修的管理352
4.4.4 培训管理352
4.4.5 维修资源的优化352
4.5 维修资源配置的实施细则352
4.5.1 员工自主维护管理细则352
4.5.2 专业维修人员管理细则352
4.5.3 外包管理员管理细则352
4.5.4 外包合同管理实施细则352
4.5.5 招标管理细则352
4.6 维修资源配置的评价激励352
4.6.1 评价的指标体系352
4.6.2 评价流程352
4.6.3 激励352
4.7 维修资源配置的案例分析353
4.8 维修资源配置的创新方向354
第5章 维修计划制订356
5.1 维修计划制订的组织职责356
5.1.1 组织职责分工356
5.1.2 系统管理356
5.2 维修计划制订的主要内容和目标管理356
5.2.1 维修计划制订的原则356
5.2.2 维修计划制订的要素356
5.2.3 维修计划制订的管理356
5.2.4 计划的目标管理357
5.3 维修计划制订的工作流程357
5.4 维修计划制订的制度规范358
5.4.1 维修计划编制原则358
5.4.2 维修计划制订358
5.4.3 维修计划的实施358
5.4.4 维修计划与信息化358
5.5 维修计划制订的实施细则358
5.5.1 维修计划编制的要素358
5.5.2 维修计划的指标体系359
5.5.3 维修计划的评价体系359
5.6 维修计划制订的评价激励359
5.7 维修计划制订的案例分析359
5.7.1 案例一359
5.7.2 案例二360
5.8 维修计划制订的创新方向361
第6章 大检修管理363
6.1 大检修管理的组织职责363
6.1.1 组织职责分工363
6.1.2 系统管理363
6.2 大检修管理的主要内容和目标计划363
6.2.1 大检修的计划管理363
6.2.2 大检修的安全管理363
6.2.3 大检修的成本管理364
6.2.4 大检修供应商的管理364
6.2.5 大检修的过程管理365
6.2.6 大检修的现场管理366
6.2.7 大检修质量管理的工作重点366
6.2.8 大检修信息化与知识资产管理368
6.3 大检修管理的工作流程368
6.4 大检修管理的制度规范369
6.4.1 设备大检修管理内容369
6.4.2 供应商管理369
6.4.3 大检修的管理评审369
6.4.4 设备技术鉴定管理369
6.4.5 开工管理370
6.4.6 档案管理370
6.5 大检修管理的实施细则370
6.5.1 大检修的管理流程要素370
6.5.2 大检修计划的制订要素370
6.5.3 供应商管理要素370
6.5.4 大检修现场管理要素370
6.5.5 设备技术质量鉴定标准要素370
6.5.6 开工管理370
6.5.7 大检修档案管理要素370
6.6 大检修管理的评价激励370
6.7 大检修管理的案例分析371
6.8 大检修管理的创新方向372
第7章 维修标准规范375
7.1 维修标准规范的组织职责375
7.1.1 组织职责分工375
7.1.2 系统管理375
7.2 维修标准规范的主要内容和目标375
7.2.1 维修标准规范的制订376
7.2.2 维修标准规范的日常管理376
7.2.3 维修标准规范的实施376
7.2.4 维修标准规范的效果评价管理376
7.2.5 维修标准规范的优化376
7.2.6 维修标准规范管理的目标377
7.3 维修标准规范的工作流程377
7.4 维修标准规范管理的制度规范378
7.4.1 设备维修作业规范378
7.4.2 维修技术规范管理378
7.4.3 维修质量验收规范管理378
7.5 维修标准规范管理制度的实施细则378
7.5.1 设备维修流程规范的要素378
7.5.2 设备维修技术标准的要素378
7.5.3 设备维修质量验收标准的要素378
7.6 维修标准规范的评价激励378
7.7 维修标准规范的案例分析379
7.7.1 案例一379
7.7.2 案例二379
7.7.3 案例三379
7.7.4 案例四379
7.8 维修标准规范的创新方向382
第8篇 六项改善持续进步篇391
引言391
第1章 六项改善培训391
1.1 六项改善培训的组织职责391
1.2 六项改善培训的主要内容和目标391
1.3 六项改善培训的工作流程392
1.4 六项改善培训的制度规范编制392
1.4.1 六项改善培训制度总则392
1.4.2 六项改善培训的评估管理394
1.4.3 内部培训责任人和外聘培训讲师管理394
1.5 六项改善培训的实施流程和工作要求394
1.6 六项改善培训的评价和激励397
1.7 六项改善培训的创新方向399
第2章 改善技巧方法研究401
2.1 改善技巧方法研究的组织职责401
2.2 改善技巧方法研究的主要内容和目标401
2.3 改善技巧方法研究的工作流程402
2.4 改善技巧方法研究的制度规范编制403
2.4.1 提案/项目申报403
2.4.2 立项审批403
2.4.3 项目实施403
2.4.4 项目过程监控404
2.4.5 项目成果申报404
2.4.6 项目成果评审404
2.4.7 项目成果发布评审404
2.4.8 成果奖励404
2.4.9 成果推广应用404
2.5 改善技巧方法研究的实施流程和工作要求404
2.6 改善技巧方法研究的评价和激励405
2.7 改善技巧方法研究案例分析405
2.8 改善技巧方法研究的创新方向406
第3章 六项改善的实施409
3.1 六项改善实施的组织职责409
3.2 六项改善实施的主要内容和目标409
3.3 六项改善实施的工作流程409
3.4 六项改善实施的制度规范编制409
3.4.1 目的409
3.4.2 适用范围409
3.4.3 小组改善实施410
3.4.4 审核410
3.4.5 改善跟踪410
3.4.6 知识共享410
3.5 六项改善实施的实施流程和工作要求410
3.6 六项改善实施的评价和激励411
3.7 六项改善实施的案例分析411
3.8 六项改善实施的创新方向412
第4章 六项改善的评价和激励414
4.1 改善评价和激励的组织职责414
4.2 改善评价和激励的主要内容和目标414
4.2.1 现金奖励标准(例)414
4.2.2 荣誉与职业奖励414
4.3 改善评价和激励的工作流程414
4.4 改善评价和激励的制度规范编制415
4.4.1 目的415
4.4.2 适用范围415
4.4.3 改善评价和激励415
4.5 改善评价和激励的实施流程和工作要求415
4.6 改善评价和激励的创新方向417
第9篇 精细备件管控模式篇422
第1章 备件管理总体框架422
1.1 备件管理的组织职责422
1.1.1 组织职责分工422
1.1.2 系统管理422
1.2 备件管理的主要内容和目标422
1.2.1 备件管理的主要内容422
1.2.2 备件管理目标423
1.3 备件管理的工作流程423
1.3.1 某石化企业备件管理工作流程423
1.3.2 某汽车企业备件管理工作流程424
1.3.3 某企业备件管理工作流程424
1.3.4 备件无库存管理业务流程424
1.3.5 网络虚拟备件库的业务流程424
1.4 备件管理的制度规范编制427
1.4.1 备件的计划控制管理427
1.4.2 备件的自制和国产化427
1.4.3 备件的修旧利废427
1.4.4 备件供应商管理427
1.4.5 备件采购和合同管理427
1.4.6 备件的验收和入库427
1.4.7 备件的库存管理427
1.4.8 备件的出库与领用427
1.4.9 备件图样和技术资料管理427
1.4.10 备件的统计管理427
1.4.11 备件的外销和报废427
1.5 备件管理的实施细则和工作要求427
1.5.1 备件计划控制的实施细则和工作要求428
1.5.2 备件自制和国产化的实施细则和工作要求428
1.5.3 备件修旧利废的实施细则和工作要求428
1.5.4 备件供应商管理的实施细则和工作要求428
1.5.5 备件采购和合同管理的实施细则和工作要求429
1.5.6 备件库存管理的实施细则和工作要求429
1.5.7 备件图样和技术资料管理的实施细则和工作要求429
1.5.8 备件统计管理的实施细则和工作要求430
1.5.9 备件外销和报废的实施细则和工作要求430
1.6 备件管理的评价和激励430
1.6.1 评价目的430
1.6.2 评价指标体系430
1.6.3 评价流程431
1.6.4 激励431
1.7 备件管理的案例分析432
1.7.1 某钢铁集团备件内部虚拟共享机制432
1.7.2 某钢厂备件国产化探索432
1.7.3 某电厂设备备件国产化的探索432
1.8 备件管理的创新方向433
1.8.1 备件供管模式的创新方向433
1.8.2 网络虚拟备件库433
1.8.3 周期备件费用最小化433
1.8.4 备件管理其他方面的创新方向434
第2章 备件分类和编码库存模型优化436
2.1 备件技术管理的组织职责436
2.1.1 构成436
2.1.2 职责436
2.2 备件技术管理的主要内容和目标436
2.2.1 主要内容436
2.2.2 管理目标437
2.3 备件属性分类判断流程437
2.4 备件技术管理的制度规范编制438
2.4.1 备件分类的原则和主要方法438
2.4.2 备件编码原则和良好编码的特点438
2.4.3 备件的ABC分类原则和标准439
2.4.4 备件3A管理的分类原则和状态类型441
2.5 备件技术管理的实施细则和注意事项442
2.5.1 备件基础技术资料整理的实施细则和注意事项442
2.5.2 备件分类的实施细则和注意事项443
2.5.3 备件编码的实施步骤和注意事项443
2.5.4 备件ABC分类法管理准则和注意事项443
2.5.5 备件3A管理的实施细则和注意事项446
2.6 备件技术管理的评价和激励446
2.6.1 评价指标446
2.6.2 激励446
2.7 备件技术管理的案例分析447
2.7.1 某钢铁企业的备件分类方式447
2.7.2 某大型电厂的备件分类管理方式447
2.7.3 某电子企业的备件编码方式447
2.7.4 某钢铁企业的备件编码方式448
2.7.5 某钢铁集团的备件编码方式449
2.7.6 某核电站备件物项编码管理案例450
2.7.7 某企业备件ABC分类管理案例451
2.7.8 某烟厂备件3A管理案例453
2.8 备件技术管理的创新方向454
第3章 备件计划的平衡与优化457
3.1 备件计划管理的组织职责457
3.1.1 构成457
3.1.2 职责457
3.2 备件计划管理的主要任务和目标458
3.2.1 主要任务458
3.2.2 目标458
3.3 备件计划管理的工作流程458
3.4 备件计划管理的制度规范编制460
3.4.1 备件计划的分类460
3.4.2 备件计划的组织申报原则460
3.4.3 备件计划的监控和调整原则460
3.4.4 备件质量异议的处理原则460
3.5 备件计划管理的实施细则和工作要求461
3.5.1 备件计划的拟订461
3.5.2 备件计划的申报方式461
3.5.3 备件计划的监控和调整方法462
3.6 备件计划管理的评价和激励462
3.6.1 评价指标体系462
3.6.2 激励462
3.7 备件计划管理案例分析462
3.7.1 某钢铁公司强化计划管理, 提高备件计划准确性462
3.7.2 某钢铁公司加强设备维护管理,减少备件申报计划463
3.7.3 某化工公司加强备件计划的动态管理463
3.8 备件计划管理的创新方向463
第4章 备件采购和供管方式优化466
4.1 备件采购管理的组织职责466
4.2 备件采购管理的主要内容和目标467
4.2.1 主要内容467
4.2.2 目标467
4.3 备件采购管理的工作流程467
4.4 备件采购管理的制度规范编制468
4.4.1 备件采购作业主要工作的目的和环节468
4.4.2 外购备件的考虑因素468
4.4.3 备件采购定价方法469
4.4.4 备件订货方式的选择原则469
4.4.5 备件集中与分散采购原则469
4.4.6 备件采购订单计划的编制要点469
4.4.7 备件采购合同条款的编制要点470
4.4.8 备件无库存管理模式的制度规范470
4.5 备件采购管理的实施细则和工作要求471
4.5.1 备件采购作业实施细则和工作要求471
4.5.2 备件采购订单计划实施细则和工作要求471
4.5.3 备件采购合同管理的实施细则和工作要求472
4.5.4 备件无库存管理的实施细则和工作要求472
4.6 备件采购管理的评价和激励473
4.6.1 评价指标体系473
4.6.2 激励473
4.7 备件采购管理案例分析473
4.7.1 用最佳性价比指导备件采购473
4.7.2 宝钢对标准备件的采购管理机制474
4.7.3 宁波钢铁采购进口备件的经验分享474
4.8 备件采购管理和供管方式的创新方向474
4.8.1 备件采购与设备前期管理474
4.8.2 备件采购模式创新475
4.8.3 联合库存备件管理模式475
4.8.4 供应商管理备件库存模式476
第5章 备件库存和领用管理优化478
5.1 备件库存和领用管理的组织职责478
5.1.1 构成478
5.1.2 职责478
5.2 备件库存和领用管理的主要内容和目标478
5.2.1 主要内容478
5.2.2 目标480
5.3 备件库存和领用管理的工作流程480
5.4 备件库存和领用的管理原则481
5.4.1 备件库存管理的基本原则481
5.4.2 选择备件存放位置的总体策略481
5.4.3 备件库位编码的作用482
5.4.4 备件出入库作业设计要点482
5.5 备件库存和领用管理的实施细则和工作要求483
5.5.1 备件库位编码的常用方法483
5.5.2 备件验货收货入库的实施细则和工作要求484
5.5.3 备件存货保管的实施细则和工作要求484
5.5.4 备件发货出库的实施细则和工作要求486
5.6 备件库存和领用管理的评价和激励487
5.6.1 评价指标体系487
5.6.2 激励487
5.7 备件库存和领用管理的案例分析487
5.8 备件库存和领用管理的创新方向487
5.8.1 旋转式备件货架应用487
5.8.2 立体备件库488
5.8.3 备件仓储可视化定置化管理489
第6章 备件修复回用和国产化492
6.1 备件修复回用和国产化的组织职责492
6.1.1 构成492
6.1.2 职责492
6.2 备件修复和国产化的主要内容和目标492
6.2.1 主要内容492
6.2.2 目标492
6.3 备件回收修复的工作流程492
6.4 备件修复和国产化的制度规范编制493
6.4.1 备件修复回用的范围493
6.4.2 备件国产化应有的意识和原则493
6.5 备件修复和国产化的实施细则和工作要求493
6.5.1 备件修复实施细则和工作要求493
6.5.2 备件国产化实施要点和工作要求494
6.6 备件修复和国产化的评价和激励496
6.6.1 评价指标体系496
6.6.2 激励496
6.7 备件修复和国产化的案例分析496
6.7.1 宝新公司管理创新让备件修复创效益496
6.7.2 安彩高科进口设备关键备件的国产化体会497
6.7.3 某企业备件国产化工作案例497
6.8 备件修复和国产化的创新方向499
6.8.1 绿色维修499
6.8.2 重视表面修复技术的应用500
第10篇 特种设备安全节能篇504
第1章 动力设备管理504
1.1 动力设备管理组织职责504
1.2 动力设备管理目标504
1.3 动力设备管理的工作流程505
1.4 动力设备管理的制度规范506
1.4.1 建立健全动力设备的各种规程并予以执行506
1.4.2 层层落实责任制,建立全员参与设备管理的体制506
1.4.3 以自主维修为核心,建立“三零”的设备管理模式506
1.4.4 建立可视化定置化管理规范507
1.5 动力设备管理实施细则507
1.5.1 动力设备安全运行管理实施细则507
1.5.2 动力设备日常点巡检管理实施细则508
1.5.3 动力设备的安全操作管理实施细则508
1.5.4 动力设备维修管理实施细则509
1.5.5 动力设备防火保卫实施细则509
1.5.6 动力设备交接班实施细则509
1.5.7 动力设备清洁卫生实施细则510
1.6 动力设备管理评价与激励510
1.6.1 评价的目的510
1.6.2 评价指标设计510
1.6.3 评价流程511
1.6.4 动力设备规范管理的评价细则511
1.6.5 激励513
1.7 动力设备管理的案例分析513
1.7.1 对原有的设备管理模式进行调研分析513
1.7.2 在动力车间建立设备管理新模式514
1.7.3 动力车间运行设备管理新模式后的效果516
1.8 动力设备管理的创新方向516
1.8.1 电力变压器状态监测技术的应用516
1.8.2 其他动力设备状态监测技术的应用517
第2章 特种设备管理519
2.1 特种设备管理组织及职责519
2.2 特种设备管理目标519
2.3 特种设备管理工作流程519
2.4 特种设备管理制度规范520
2.4.1 特种设备的作业人员及其相关管理人员的资质520
2.4.2 特种设备的制造、安装、改造及维修521
2.4.3 特种设备的使用521
2.4.4 检验检测522
2.4.5 特种设备的事故预防和调查处理522
2.4.6 特种设备的行政许可变更522
2.5 特种设备管理实施细则522
2.6 特种设备管理评价与激励525
2.6.1 评价目的525
2.6.2 评价指标体系525
2.6.3 评价范畴526
2.6.4 标准项目及评价细则526
2.6.5 激励528
2.7 特种设备管理案例分析528
2.7.1 事故概况529
2.7.2 事故发生过程529
2.7.3 事故调查分析529
2.7.4 事故调查结论530
2.7.5 事故处理530
2.8 特种设备管理创新方向531
2.8.1 特种设备管理信息化531
2.8.2 特种设备管理新技术的应用531
第3章 节能减排管理533
3.1 节能减排管理组织及职责533
3.1.1 节能减排工作领导小组533
3.1.2 节能减排办公室533
3.1.3 设备管理部门533
3.1.4 安全环保部门534
3.1.5 基建管理部门534
3.1.6 生产管理部门534
3.1.7 财务审计部门534
3.1.8 技术管理部门535
3.1.9 行政部门535
3.1.10 人力资源部门535
3.2 节能减排管理主要内容和目标535
3.2.1 节能减排管理主要内容535
3.2.2 节能减排管理目标535
3.3 节能减排管理工作流程535
3.4 节能减排管理制度规范536
3.4.1 成立节能减排领导小组的文件537
3.4.2 明确节能减排目标与责任的文件537
3.4.3 节能减排管理制度(规定)537
3.4.4 节能减排管理其他方面的制度(规定)537
3.5 节能减排管理实施细则537
3.5.1 节能减排的方针与目标指标537
3.5.2 节能减排基础工作的管理537
3.5.3 节能减排统计监测与报告539
3.5.4 节能减排规划544
3.5.5 节能减排考核544
3.5.6 节能产品认证与能源效率标识544
3.6 节能减排管理评价与激励545
3.6.1 工业企业节能减排主要指标解释545
3.6.2 节能减排目标责任评价考核546
3.7 节能减排管理案例分析548
3.7.1 企业概况548
3.7.2 清洁生产的宣传548
3.7.3 审核重点分析549
3.7.4 清洁生产审核绩效550
3.8 节能减排管理创新方向550
3.8.1 合同能源管理550
3.8.2 再制造551
第11篇 技术改造更新拓展篇556
第1章 设备技术经济分析556
1.1 设备技术经济分析组织职责556
1.1.1 设备管理部门556
1.1.2 设备管理部门负责人556
1.1.3 设备使用单位556
1.1.4 公司生产主管领导(总经理)556
1.2 设备技术经济分析原则556
1.3 设备技术经济分析工作流程556
1.4 设备技术经济分析方法557
1.4.1 设备更新的技术经济分析方法557
1.4.2 设备技术改造的技术经济分析方法557
1.4.3 设备更新、技术改造综合技术经济分析方法557
1.5 设备技术经济分析实施细则557
1.5.1 有形磨损的更新决策557
1.5.2 无形磨损的更新决策558
1.5.3 生产能力不足时的更新决策558
1.5.4 设备总费用现值比较558
1.5.5 设备技术改造的效益评价558
1.5.6 总使用成本比较法计算公式558
1.5.7 指标对比法使用的参数和符号559
1.6 设备技术经济分析评价激励560
1.7 设备技术经济分析案例560
1.7.1 有形磨损的更新决策560
1.7.2 生产能力不足时的更新决策560
1.7.3 设备总费用现值比较560
1.7.4 总使用成本比较法561
1.8 设备技术经济分析创新方向562
第2章 技改前期准备564
2.1 技改前期准备组织职责564
2.2 技改前期准备目标564
2.3 技改前期准备工作流程564
2.4 技改前期准备规范要求564
2.4.1 安全规范564
2.4.2 标准规范564
2.4.3 环保规范564
2.4.4 产业规范564
2.5 技改前期准备实施细则564
2.5.1 改造思路的确定564
2.5.2 改造前的技术准备工作565
2.6 技改前期准备评价激励566
2.7 技改前期准备案例566
2.8 技改前期准备创新方向566
第3章 技改实施568
3.1 技改实施组织职责568
3.1.1 技改项目负责人568
3.1.2 技改项目小组568
3.1.3 技改施工单位568
3.1.4 公司生产主管领导(总经理)568
3.2 技改实施目标568
3.3 技改实施工作流程568
3.4 技改实施规范要求569
3.5 技改实施细则569
3.5.1 原设备的全面保养569
3.5.2 保留的机械电气部分最佳化调整569
3.5.3 改造部分拆除569
3.5.4 合理安排改造部分的位置及相互连接569
3.5.5 调试569
3.5.6 验收及后期工作569
3.6 技改实施评价激励570
3.7 技改实施案例570
3.8 技改实施创新方向570
第4章 技改效果跟踪评估572
4.1 技改效果跟踪评估组织职责572
4.1.1 设备使用单位572
4.1.2 评估小组572
4.1.3 设备管理部门负责人572
4.1.4 公司生产主管领导572
4.2 技改效果跟踪评估572
4.2.1 设备改造目标572
4.2.2 技改效果跟踪评估目的572
4.3 技改效果跟踪评估工作流程572
4.4 技改效果跟踪评估规范要求572
4.5 技改效果跟踪评估实施细则572
4.5.1 技改效果跟踪评估内容572
4.5.2 技改评价总结574
4.6 技改效果跟踪评估评价激励574
4.7 技改效果跟踪评估案例574
4.8 技改效果跟踪评估创新方向574
第12篇 精益TnPM体系融合篇581
第1章 精益TnPM体系融合总体框架581
1.1 精益TnPM体系融合的组织职责581
1.1.1 组织职责分工581
1.1.2 系统管理581
1.2 精益TnPM体系融合的目标581
1.2.1 目标581
1.2.2 手段581
1.3 精益TnPM体系融合工作流程581
1.4 精益TnPM体系融合管理制度规范582
1.4.1 精益TnPM规划管理规定582
1.4.2 精益TnPM体系融合实施管理规定582
1.5 精益TnPM体系融合实施细则582
1.6 精益TnPM体系融合的评价与激励582
1.6.1 评价范畴582
1.6.2 评价指标设计583
1.6.3 评价的流程583
1.6.4 激励583
1.7 精益TnPM体系融合案例分析583
1.7.1 背景介绍583
1.7.2 规划583
1.7.3 效果583
1.7.4 不足584
1.8 精益TnPM体系融合的创新方向584
第2章 精益TnPM体系融合生产线改造586
2.1 生产线改造的组织职责586
2.1.1 组织职责分工586
2.1.2 系统管理586
2.2 生产线改造的目标586
2.2.1 目标586
2.2.2 手段586
2.3 生产线改造工作流程586
2.4 生产线改造管理制度规范586
2.4.1 生产线改造规划管理规定586
2.4.2 生产线改造实施管理规定586
2.5 生产线改造实施细则587
2.5.1 单件流(小批量流)实施细则587
2.5.2 看板生产方式实施细则587
2.5.3 均衡生产实施细则587
2.5.4 标准作业实施细则588
2.5.5 产线平衡实施细则588
2.5.6 多能工培养实施细则588
2.5.7 “水蜘蛛”作业实施细则588
2.5.8 “安灯”实施细则588
2.5.9 设备布局实施细则588
2.6 生产线改造的评价与激励588
2.6.1 评价指标设计588
2.6.2 评价的流程588
2.6.3 激励589
2.7 生产线改造案例分析589
2.7.1 背景589
2.7.2 改善前后数据对比589
2.8 生产线改造创新方向589
第3章 精益TnPM体系融合快速换模591
3.1 快速换模的组织职责591
3.1.1 规划与决策591
3.1.2 系统管理591
3.2 快速换模的目标591
3.2.1 目标591
3.2.2 实现目标的手段591
3.3 快速换模管理工作流程591
3.4 快速换模管理制度规范592
3.5 快速换模管理实施细则592
3.6 快速换模评价与激励592
3.6.1 评价指标592
3.6.2 评价流程592
3.6.3 激励592
3.7 快速换模案例分析592
3.7.1 背景592
3.7.2 快速换模的主要实施步骤592
3.7.3 效果592
3.7.4 不足592
3.8 快速换模的创新方向593
第4章 精益TnPM体系融合自动化595
4.1 实施自动化的组织职责595
4.1.1 组织职责分工595
4.1.2 系统管理595
4.2 自动化的目标595
4.2.1 目标595
4.2.2 达成手段595
4.3 自动化工作流程595
4.4 自动化管理制度规范596
4.5 自动化实施细则596
4.6 自动化的评价与激励596
4.6.1 评价指标596
4.6.2 评价流程596
4.6.3 激励597
4.7 自动化案例分析597
4.7.1 案例分析一597
4.7.2 案例分析二597
4.7.3 案例分析三597
4.8 自动化的创新方向597
第5章 精益TnPM体系融合动作改善600
5.1 动作改善的组织职责600
5.1.1 组织职责分工600
5.1.2 系统管理600
5.2 动作改善的目标600
5.3 动作改善工作流程600
5.4 动作改善管理制度规范601
5.5 动作改善实施细则601
5.6 动作改善评价与激励602
5.6.1 评价指标设计602
5.6.2 评价的流程602